The powertrain has long been at the center of vehicle performance. But as Electric Vehicles (EVs) transition from early adopters to everyday roads, its definition is undergoing a transformation. No longer a complex arrangement of pistons, crankshafts, and fuel injectors, today’s EV powertrain is a tightly integrated system of electric motors, high-voltage components, and intelligent controllers—all working together to deliver smooth, silent, and highly efficient power to the wheels.
What makes this transformation so remarkable isn’t just the switch from gasoline to electrons. It’s the way the entire structure of propulsion has changed—simplified in some ways, yet more precise and software-driven than ever before. Understanding how an EV powertrain functions isn’t just for engineers or enthusiasts anymore; it’s essential for anyone who wants to make sense of the rapidly evolving electric vehicle landscape.
This article explores the anatomy of an EV powertrain—its key components, how it works, the different configurations in use today, and how it compares to traditional internal combustion drivetrains. From urban commuters to high-performance electric sedans, everything starts with the powertrain.
What Is an EV Powertrain?
At its core, a powertrain refers to all the components in a vehicle that generate power and deliver it to the wheels. In traditional vehicles, this includes the engine, transmission, driveshafts, differentials, and axles. In an electric vehicle (EV), however, the powertrain is dramatically different—simpler in mechanical structure, but far more sophisticated in terms of control and energy management.
An EV powertrain typically consists of an electric motor, an inverter, a reduction gearbox or transmission, and a high-voltage battery system. These components work in harmony to convert stored electrical energy into mechanical motion. Unlike combustion engines that require multiple moving parts and complex gear systems, EV powertrains often operate with fewer mechanical losses, providing immediate torque and smoother acceleration.
Beyond efficiency, the EV powertrain plays a crucial role in how the vehicle feels and performs. It governs not only acceleration and regenerative braking but also energy recovery, thermal management, and—through integrated software—dynamic driving behavior. Whether in a compact city EV or a high-performance electric sports car, the powertrain defines the vehicle’s character.
Perhaps the most revolutionary aspect of the EV powertrain is its ability to operate through intelligent electronic control, making real-time adjustments to maximize efficiency and driving comfort. This is not just a drivetrain replacement—it’s a complete rethinking of how vehicles move, behave, and interact with energy.
Key Components of an EV Powertrain
The EV powertrain might appear simpler than its internal combustion counterpart, but each component is carefully engineered to deliver seamless, high-efficiency propulsion. Let’s break down the key building blocks that make up a modern electric vehicle’s powertrain.
Electric Motor
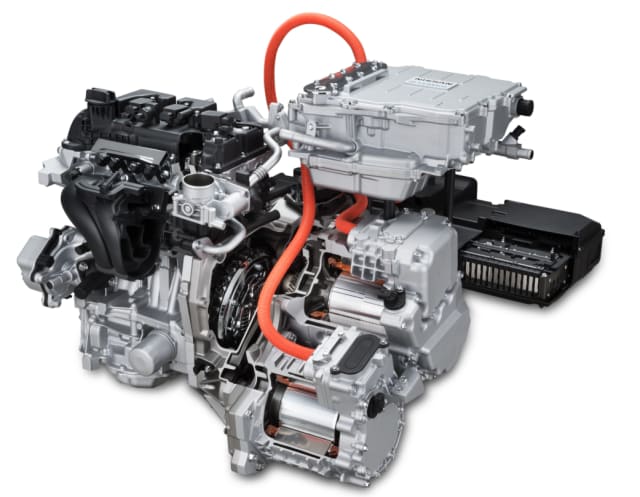
The electric motor is the primary mover in an EV, converting electrical energy from the battery into mechanical motion. Unlike combustion engines that need to rev up to produce torque, electric motors provide instant torque, which translates into rapid acceleration and smoother driving.
There are several types of motors used in EVs, including:
- Permanent Magnet Synchronous Motors (PMSM) – Highly efficient and commonly used in modern EVs.
- Induction Motors (IM) – Robust and cost-effective, famously used in early Tesla models.
- Brushless DC Motors (BLDC) – Found in smaller or budget EV applications.
Electric motors are compact, responsive, and require minimal maintenance due to fewer moving parts. Their design allows for flexible placement in the vehicle—either centrally or directly within the wheels.
Inverter
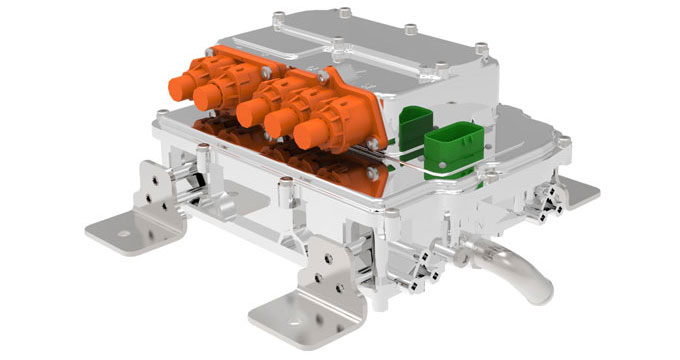
The inverter is the brain behind the motor. It converts the DC (Direct Current) stored in the battery into AC (Alternating Current) required by most electric motors. But more than just a power converter, the inverter also controls motor speed and torque by adjusting the frequency and amplitude of the current.
Modern inverters use semiconductor technology such as IGBT or SiC (silicon carbide) switches to optimize efficiency, switching speed, and heat resistance. In many EVs, the inverter is integrated with the motor housing to reduce weight and wiring complexity.
Transmission (Gearbox)
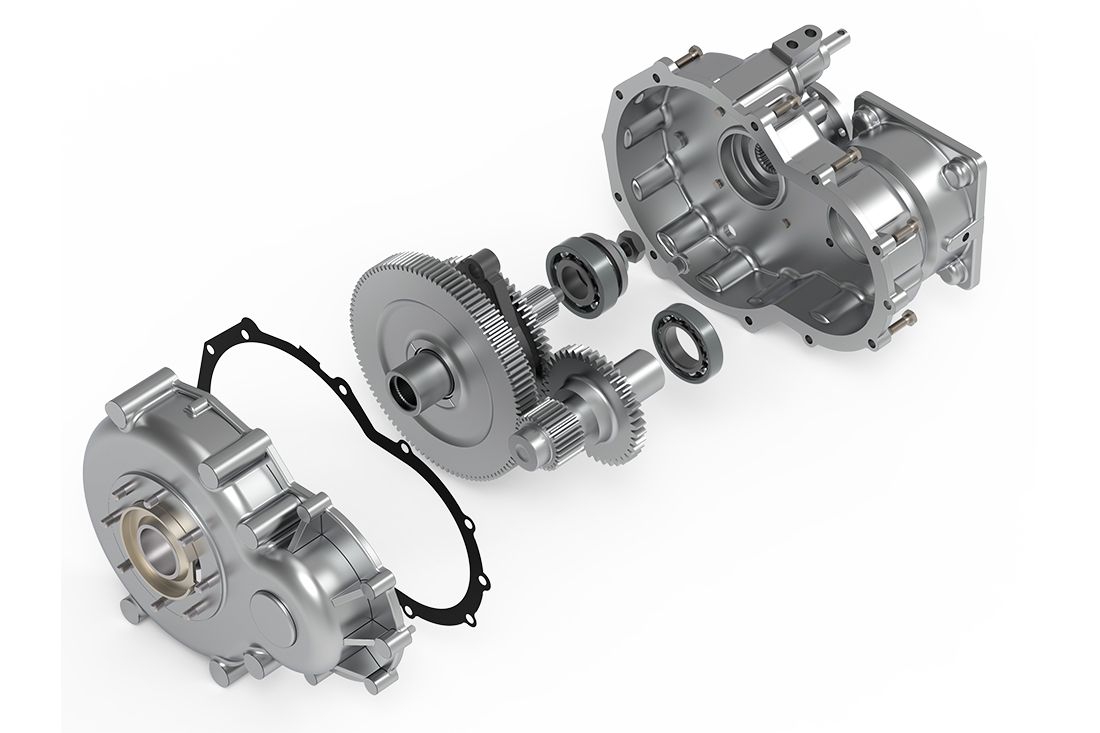
Unlike traditional vehicles with multi-speed transmissions, most EVs use a single-speed reduction gear. This is because electric motors can operate efficiently across a wide RPM range without the need for shifting gears.
However, some performance EVs (like the Porsche Taycan) use a two-speed transmission to enhance acceleration and highway efficiency. The transmission connects the motor to the drive wheels and ensures the torque is delivered smoothly and effectively.
In direct-drive configurations—common in simpler EV platforms—the motor is connected directly to the wheels with minimal mechanical linkage, reducing energy loss.
Battery Pack & Energy Storage

The battery is the energy reservoir of the EV powertrain. It typically uses lithium-ion chemistry, though solid-state and LFP (lithium iron phosphate) technologies are also gaining popularity.
Battery packs are made of modules and cells configured to store hundreds of volts (commonly 400V or 800V systems). Located in the vehicle floor to optimize weight distribution, the battery feeds power to the motor via the inverter and supports regenerative energy recovery.
Battery performance is directly tied to range, charging time, and overall powertrain efficiency, making it a critical part of EV engineering.
Power Electronics & Controllers

Power electronics manage the flow of energy throughout the EV. This includes devices like:
- DC-DC Converter – Steps down high-voltage battery current to low-voltage (12V or 48V) systems for lights, infotainment, and accessories.
- On-Board Charger (OBC) – Converts AC from a EV charging station into DC to recharge the battery.
- Motor Controller – Governs how the motor behaves in response to accelerator input, brake regeneration, and drive mode settings.
These systems are central to energy efficiency, system protection, and driver experience.
Thermal Management System
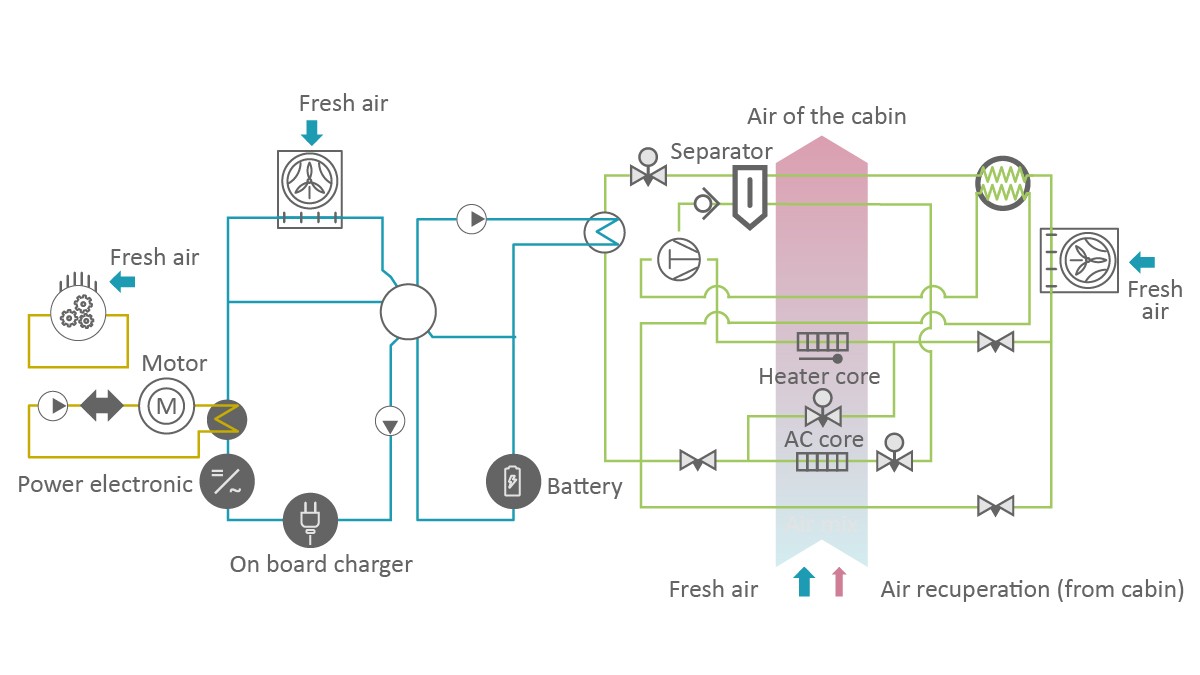
As with any high-performance system, managing heat is essential. The thermal management system regulates the temperature of the battery, motor, inverter, and electronics. This ensures components operate within optimal temperature ranges for performance, safety, and longevity.
Many EVs use liquid cooling systems, often integrated into the powertrain to maintain stable operation under varying load conditions. Advanced EV platforms also use heat pumps to improve overall energy efficiency, especially in colder climates.
How an EV Powertrain Works
At a glance, the operation of an EV powertrain may seem simple—electricity flows from the battery to the motor, and the vehicle moves. But behind the scenes, a highly synchronized system of hardware and software ensures this process happens safely, efficiently, and responsively under varying driving conditions.
Step 1: Energy Supply from the Battery
Everything begins with the high-voltage battery pack, which stores the electrical energy used to drive the vehicle. When the driver presses the accelerator, the Battery Management System (BMS) ensures the correct amount of power is delivered based on input, charge level, temperature, and other real-time factors.
Step 2: Inverter Converts DC to AC
The battery outputs direct current (DC), but most electric motors operate on alternating current (AC). The inverter takes this DC energy and precisely transforms it into AC, adjusting frequency and voltage to control motor speed and torque. It’s effectively the translator between static stored energy and dynamic motion.
Step 3: Motor Drives the Wheels
Once powered, the electric motor generates a rotating magnetic field that drives the rotor and produces torque. Because of the motor’s wide operational range, the EV can accelerate from a stop or cruise at high speeds without gear shifting, especially in single-speed configurations. Torque is delivered instantly, making acceleration quick and smooth.
Step 4: Power Transfer via Transmission
The transmission (typically a reduction gear) connects the motor to the wheels. It reduces the motor’s high RPM output into usable wheel speed and torque. In dual-motor or all-wheel-drive (AWD) EVs, this process happens simultaneously in front and rear axles for better traction and performance.
Step 5: Regenerative Braking Feeds Energy Back
One of the most innovative aspects of the EV powertrain is regenerative braking. When the driver decelerates or applies the brakes, the electric motor reverses operation and acts as a generator, converting kinetic energy from the wheels back into electrical energy, which is stored in the battery. This extends driving range and reduces wear on the brake pads.
Step 6: Control Systems Manage Everything
A network of ECUs (Electronic Control Units), sensors, and software continuously monitor and manage the system. From optimizing motor efficiency to protecting the battery from overheating or over-discharging, the software layer is vital. Advanced systems also adapt torque distribution, throttle response, and braking characteristics based on driving conditions.
The result is a fluid, responsive, and intelligent driving experience, where performance, range, and efficiency are constantly balanced in real time. This deep integration of components and control logic is what truly sets EV powertrains apart from traditional drivetrains.
EV Powertrain Configurations and Drive Types
Not all EVs are built the same beneath the surface. One of the most flexible aspects of electric vehicle design is how the powertrain can be configured to suit different driving styles, performance levels, and use cases. Unlike combustion-engine layouts, which are often limited by mechanical constraints, EV powertrains offer a modular and space-efficient architecture. Let’s explore the most common drive types.
Front-Wheel Drive (FWD)

In Front-Wheel Drive EVs, the electric motor is mounted on the front axle, delivering power directly to the front wheels. This layout is commonly found in compact and budget-friendly EVs due to its simplicity, lower manufacturing cost, and efficient packaging.
Advantages:
- Easier to package batteries and cabin space
- Lower production and assembly cost
- Predictable understeer driving behavior
Limitations:
- Less balanced weight distribution
- Moderate performance in slippery conditions
FWD is ideal for urban commuting and daily driving where performance isn’t the top priority.
Rear-Wheel Drive (RWD)

Rear-Wheel Drive configurations place the electric motor at the rear axle, propelling the vehicle from behind. This setup provides better weight balance and a more dynamic driving experience, especially when the battery pack is mounted centrally.
Advantages:
- Improved acceleration and handling dynamics
- Better load transfer under acceleration
- Common in performance-oriented EVs (e.g., Tesla Model 3 RWD)
Limitations:
- Slightly more complex drivetrain packaging
- May struggle in icy or wet conditions without traction control
RWD is often favored in mid-range to high-performance EVs, balancing sportiness and efficiency.
All-Wheel Drive (AWD) and Dual Motor Setup
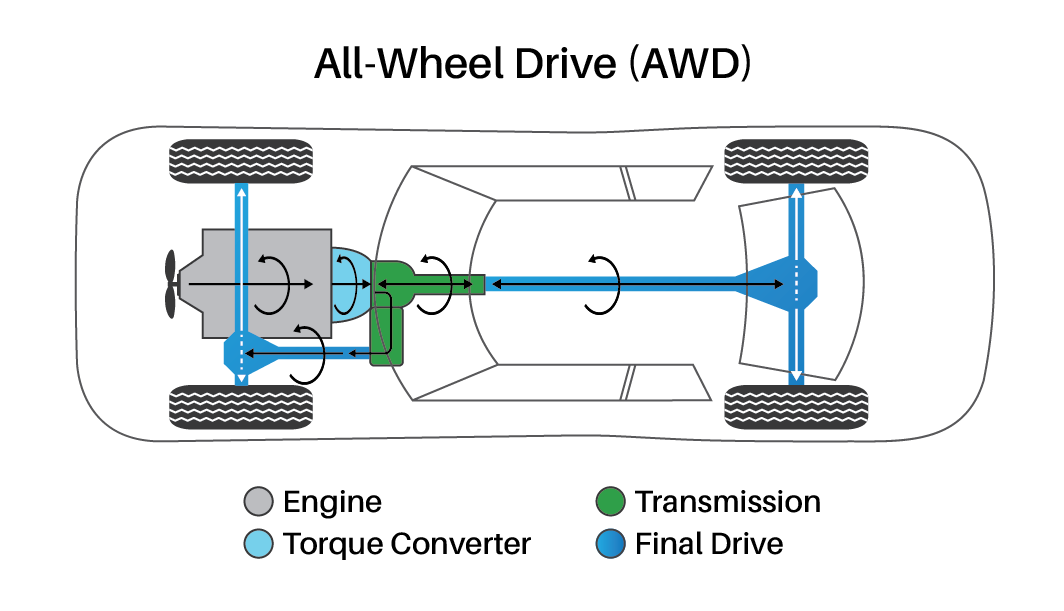
All Wheel Drive (AWD) EVs use two or more electric motors, typically one on each axle. This provides power to all four wheels, enhancing traction, acceleration, and control. Many premium EVs employ this configuration for optimal performance.
Advantages:
- Superior traction in all weather conditions
- Faster acceleration (thanks to power split and torque vectoring)
- Independent torque control for front and rear motors
Limitations:
- Higher cost and complexity
- Slight reduction in range due to increased energy demand
AWD setups are popular in crossovers, SUVs, and high-performance sedans, where all-weather capability and responsiveness are desired.
In-Wheel Motor Systems
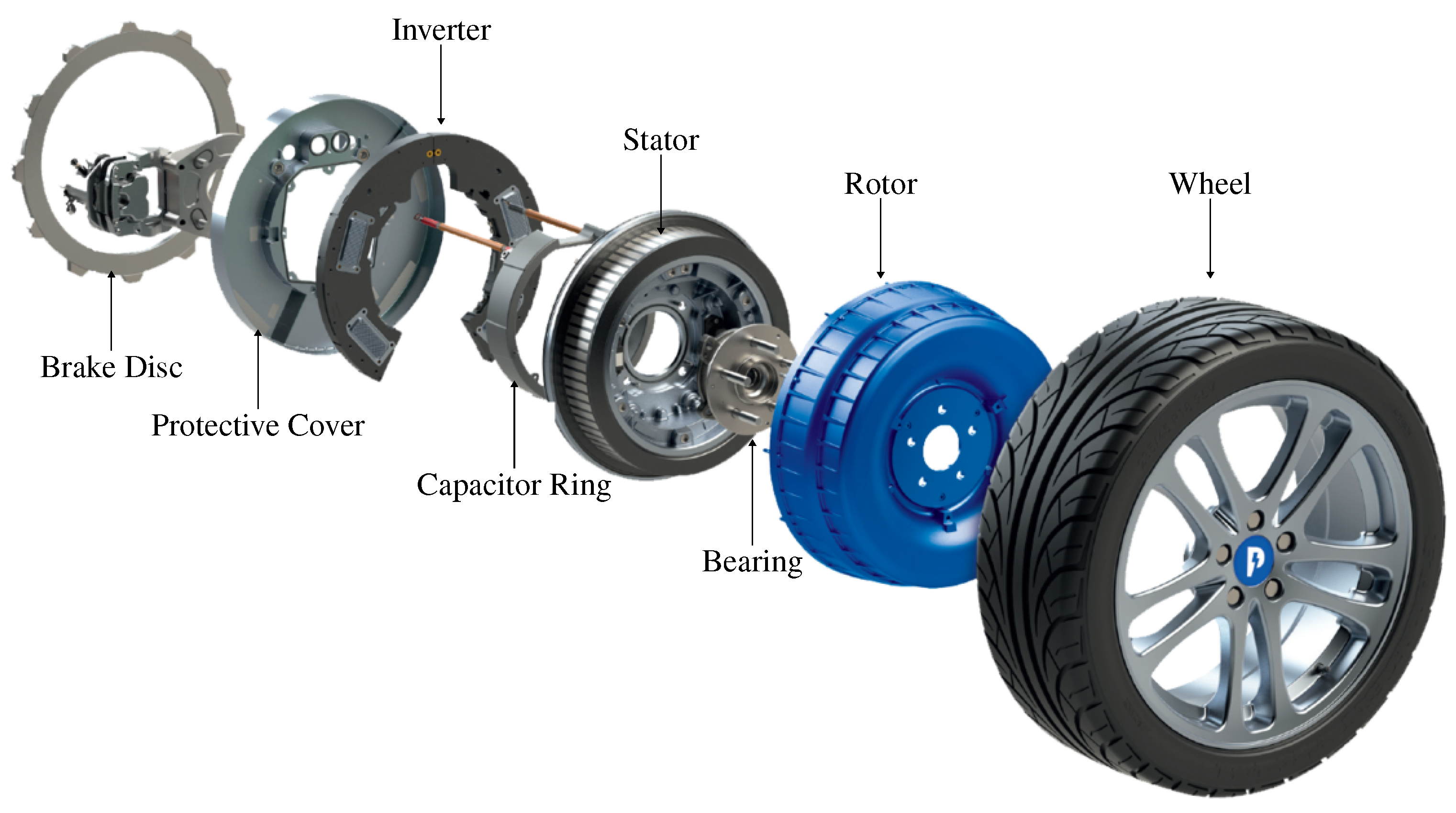
An emerging innovation in EV powertrain design is the in-wheel motor system, where the electric motor is embedded directly into each wheel hub. This eliminates the need for a central drivetrain or transmission entirely.
Advantages:
- Extreme space efficiency
- Precise wheel-level torque control
- Potential for advanced torque vectoring and off-road capabilities
Challenges:
- Added unsprung mass affecting suspension and ride comfort
- Higher mechanical stress and thermal management complexity
- Still under active development; not yet mainstream
In-wheel motors hold promise for next-generation EVs, particularly in niche segments like robotics, autonomous car shuttles, and ultra-compact urban vehicles.
Each configuration offers trade-offs between performance, efficiency, cost, and drivability. The modular nature of electric powertrains allows manufacturers to tailor their vehicles to specific markets and driving demands, making the layout a critical design decision.
EV Powertrain vs ICE Drivetrain
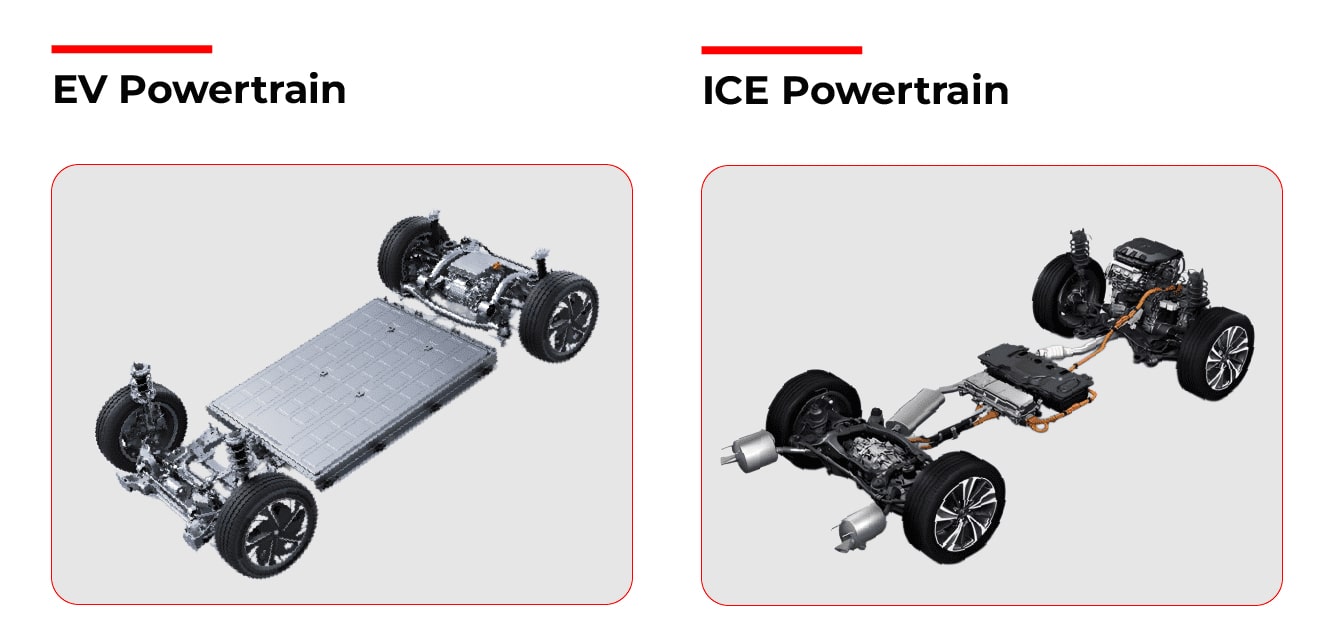
The shift from internal combustion engines (ICE) to electric vehicles isn’t just about the fuel source—it’s a transformation in how vehicles are built, how they operate, and how they’re maintained. Comparing the EV powertrain to a traditional ICE drivetrain highlights just how fundamentally different these two propulsion systems really are.
Structural Differences
In a conventional ICE vehicle, the powertrain includes the engine, multi-speed transmission, clutch or torque converter, driveshafts, differential, and exhaust system. These components require precise mechanical coordination and regular maintenance.
EVs, on the other hand, strip the powertrain down to fewer moving parts: typically a battery, an inverter, a single-speed transmission, and an electric motor. This simplicity translates to less mechanical wear and fewer failure points over time.
Efficiency and Performance
EV powertrains are significantly more efficient than ICE counterparts. While a gasoline engine converts only about 20–30% of the fuel’s energy into motion, electric motors can achieve 85–95% efficiency. Instant torque and smooth acceleration are inherent characteristics of EVs, requiring no gear shifting.
Moreover, regenerative braking in EVs allows energy to be recovered during deceleration—a feature ICE drivetrains simply can’t match.
Maintenance and Longevity
EVs benefit from:
- No oil changes
- No spark plugs or timing belts
- Minimal brake wear due to regenerative braking
- Fewer fluid replacements
This leads to lower maintenance costs and longer component lifespans.
Software Integration
Unlike ICE systems that are largely mechanical, EV powertrains are software-defined, meaning that performance, efficiency, and even the “feel” of the vehicle can be adjusted via over-the-air updates. This adaptability gives EVs a long-term advantage as technology evolves.
Table: EV Powertrain vs ICE Drivetrain
Feature | EV Powertrain | ICE Drivetrain |
---|---|---|
Energy Source | Battery (Electricity) | Fuel (Gasoline/Diesel) |
Main Components | Electric motor, inverter, battery, gearbox | Engine, transmission, exhaust, fuel system |
Efficiency | 85–95% | 20–30% |
Torque Delivery | Instant | Delayed (engine needs revving) |
Transmission | Usually single-speed | Multi-speed with clutch/torque converter |
Regenerative Braking | Yes | No |
Maintenance | Minimal (few moving parts) | Frequent (oil, belts, filters) |
Software Control | Extensive (OTA updates possible) | Limited |
Emissions | Zero tailpipe emissions | CO₂, NOx, particulate matter |
Noise and Vibration | Very low | High (mechanical and combustion noise) |
This comparison reinforces that EV powertrains are not just an evolution—they are a clean break from traditional automotive engineering, offering a simpler, smarter, and more efficient path forward.
Innovations in EV Powertrain Technology
As electric vehicle adoption accelerates, so does the pace of innovation within their powertrain systems. While the core components—motor, inverter, battery—remain central, the technologies surrounding them are evolving rapidly to improve efficiency, performance, scalability, and integration with smart systems.
Silicon Carbide (SiC) Inverters
One of the most significant advances in power electronics is the use of silicon carbide (SiC) materials in inverters. Compared to traditional silicon-based components, SiC inverters:
- Switch faster with less energy loss
- Operate at higher temperatures
- Enable smaller, lighter cooling systems
These characteristics lead to greater energy efficiency and reduced charging times. Automakers like Tesla and Lucid Motors have already adopted SiC to improve vehicle range and acceleration.
Modular and Lightweight Powertrain Design
Newer EV platforms are moving toward modular powertrain architectures, where components like the motor, inverter, and gearbox are integrated into compact units known as “e-axles” or “drive units.” These modules simplify vehicle design, reduce weight, and allow easy scaling across different models.
By minimizing complexity and mass, manufacturers can increase range and improve production efficiency without sacrificing performance.
Software-Defined Powertrains
Unlike traditional vehicles that rely heavily on mechanical linkages, EV powertrains are controlled almost entirely by software. This includes:
- Torque vectoring between multiple motors
- Smart energy usage depending on driving mode
- Adaptive regenerative braking profiles
The shift toward software-defined vehicles (SDVs) means that many aspects of the powertrain—throttle response, brake feel, drivetrain balance—can be updated or optimized over-the-air, post-sale.
Vehicle-to-Grid (V2G) Integration
Next-generation EV powertrains are being designed with bidirectional charging in mind, enabling Vehicle-to-Grid (V2G) and Vehicle-to-Home (V2H) applications. With proper infrastructure, EVs can:
- Supply power back to the grid during peak demand
- Serve as backup generators for homes
- Optimize grid efficiency through energy load balancing
This transforms EVs from just transportation tools into active energy assets.
Advanced Thermal and Energy Management Systems
Thermal management is critical to both performance and safety. EV powertrains are now incorporating:
- Multi-zone cooling circuits (for batteries, inverters, motors)
- Heat pumps to recycle waste heat
- Predictive thermal models powered by AI
These systems ensure consistent performance, reduce charging time, and protect component longevity.
AI and Predictive Optimization
Artificial intelligence is increasingly being embedded in EV powertrain systems to:
- Predict driving behavior and adjust energy flow
- Optimize motor output based on terrain and traffic
- Extend battery life through smart charging routines
As data becomes more central to driving, the powertrain is evolving into a responsive, intelligent system, tailored in real-time to the user and environment.
These innovations mark a shift from merely electrifying the old drivetrain model to reimagining propulsion from the ground up. With each leap in efficiency, intelligence, and flexibility, the EV powertrain is solidifying its role as the future standard in automotive engineering.
Challenges in EV Powertrain Development
Despite the remarkable progress in electric vehicle technology, building and refining EV powertrains remains a complex engineering challenge. From materials to control systems, each advancement introduces new trade-offs in cost, durability, and real-world usability. Understanding these challenges offers insight into why EVs are still evolving—and what might shape their next generation.
Thermal Management Under High Loads
Electric motors, inverters, and batteries all generate heat, especially under rapid acceleration or fast charging. If not managed properly, this heat can degrade performance, reduce efficiency, or even shorten the lifespan of key components.
Advanced cooling systems are essential, but they increase cost and design complexity. High-performance EVs often require multi-layer thermal management systems, which add weight and demand careful system integration.
Rare Earth Material Dependency
Most high-efficiency electric motors use rare earth elements like neodymium and dysprosium in their permanent magnets. These materials are:
- Expensive to source and process
- Concentrated in supply from a few countries
- Environmentally and geopolitically sensitive
The industry is exploring magnet-free or reduced-RE motor designs, but currently, these remain more costly or less efficient in certain use cases.
Packaging Constraints
While EVs offer greater freedom in design compared to ICE vehicles, the powertrain still faces tight packaging challenges, especially in compact or performance models. Engineers must:
- Balance battery placement with weight distribution
- Fit drive units without compromising cabin or cargo space
- Manage crash safety zones around high-voltage systems
As EVs shrink or diversify in shape (crossovers, trucks, city EVs), these constraints become more critical.
Cost of High-Performance Components
Cutting-edge powertrain parts—like SiC inverters, high-density batteries, or dual-motor AWD systems—are expensive. While premium EVs can absorb these costs, affordability remains a major obstacle in the mass market.
Balancing innovation with cost-effective manufacturing is one of the defining challenges for automakers competing in the global EV space.
Complex Software and System Integration
Modern EV powertrains are driven by software layers that manage motor behavior, battery safety, torque distribution, and regenerative braking. But this shift toward digital control introduces its own risks:
- Software bugs or firmware flaws can impact drivability or safety
- System updates must be secure and reliable over time
- Diagnosing failures can be harder than with mechanical systems
Additionally, ensuring cybersecurity for over-the-air updates and data-driven control is becoming a critical priority.
While these challenges are significant, they are far from insurmountable. In fact, many of today’s innovations—like solid-state batteries, AI-assisted control systems, and rare-earth-free motors—are being developed directly in response to these hurdles. The EV powertrain remains a frontier of automotive technology, where every limitation is also an opportunity for evolution.
Future Trends in Powertrain Design
As electric vehicle technology matures, the powertrain continues to evolve beyond basic functionality into a more intelligent, adaptable, and sustainable system. Manufacturers, engineers, and innovators are already pushing toward the next wave of advancements that will define how EVs perform, integrate with infrastructure, and meet the needs of tomorrow’s mobility landscape.
Shift Toward Software-Defined Vehicles
The rise of software-defined vehicles (SDVs) is reshaping how powertrains are designed and deployed. Instead of relying solely on fixed mechanical characteristics, SDVs allow manufacturers to:
- Adjust power delivery and torque characteristics via software
- Offer customizable driving modes, even post-purchase
- Optimize efficiency through real-time updates and AI learning
This trend enables greater flexibility, giving manufacturers and drivers the ability to fine-tune vehicle behavior based on region, climate, or even individual driving style.
Integration with Advanced Driver Assistance Systems (ADAS)
Future EV powertrains will not function in isolation. They’ll integrate deeply with ADAS and autonomous driving systems, enabling coordinated control between propulsion, steering, braking, and navigation.
For example:
- Predictive energy deployment based on traffic or terrain
- Adaptive regenerative braking tied to sensor inputs
- Torque vectoring based on vehicle stability and sensor feedback
This fusion of drivetrain and autonomy creates safer, more energy-efficient driving, especially in urban or high-speed environments.
Scalable, Platform-Based Architectures
Automakers are increasingly moving toward modular EV platforms (e.g., GM’s Ultium, Hyundai’s E-GMP, Volkswagen’s MEB) that allow the same powertrain modules to be used across multiple Vehicle Types—from hatchbacks to SUVs to trucks.
These platforms simplify manufacturing and support:
- Variable battery sizes and motor outputs
- FWD, RWD, or AWD configurations
- Faster product development cycles
This platform unification is expected to significantly reduce costs and improve access to EVs globally.
Use of Solid-State Components
Solid-state batteries often receive the spotlight, but solid-state electronics in the powertrain are just as transformative. From solid-state relays to integrated motor-drive units, these components:
- Reduce weight and size
- Offer higher thermal tolerance
- Enhance long-term reliability
Expect future powertrain units to become more compact, lighter, and integrated, helping EVs gain range without increasing battery capacity.
Predictive Power Management
EVs of the future will use data-driven algorithms to anticipate how and when power should be deployed, rather than simply reacting to driver input. Using inputs such as:
- Navigation data
- Traffic patterns
- Weather and road conditions
the powertrain will dynamically adjust performance and energy use, reducing waste and enhancing driver experience. Think of it as a system that “thinks ahead” to deliver the right amount of power—before you even need it.
Bi-Directional Energy Systems and Grid Integration
As EVs increasingly support bidirectional charging (V2G and V2H), the powertrain will no longer be a one-way energy consumer. It will become a participant in the broader energy ecosystem:
- Discharging to the grid during peak hours
- Supplying power to homes during outages
- Charging more efficiently based on grid demands
This transition positions EVs as energy hubs, not just vehicles, and powertrain components will need to be robust and flexible enough to handle multi-directional energy flow.
These trends point toward an EV future that’s more than just electric—it’s intelligent, connected, modular, and adaptive. As innovation continues, the powertrain will remain at the center of that transformation, shaping how we move, power, and interact with vehicles for decades to come.
Conclusion
The EV powertrain is more than just a collection of parts that move an electric vehicle—it is the technological core that defines how these vehicles perform, behave, and evolve. Unlike internal combustion drivetrains built around fuel-burning engines and mechanical complexity, EV powertrains embrace a new design philosophy: one centered on simplicity, precision, and digital intelligence.
By understanding the components—electric motor, inverter, battery, and control electronics—and how they work together, we get a clearer picture of why EVs are not just an alternative to gasoline cars, but a leap forward in automotive engineering. The ability to deliver instant torque, reclaim energy through regenerative braking, and adapt behavior through software updates puts EV powertrains in a category of their own.
As new innovations emerge—from silicon carbide inverters and in-wheel motors to bidirectional energy systems and AI-based optimization—the powertrain will remain a dynamic platform for progress. Whether you’re a driver, a tech enthusiast, or someone simply curious about the future of mobility, knowing how the EV powertrain works is a window into the future of transportation—cleaner, smarter, and fundamentally more efficient.
FAQ About EV Powertrains
What is the powertrain of an EV?
In an electric vehicle (EV), the powertrain refers to the entire system responsible for generating and delivering power to the wheels. This includes the electric motor, inverter, transmission (usually single-speed), and the high-voltage battery. Unlike traditional vehicles, there’s no engine or fuel system—everything is driven by electricity, making the EV powertrain simpler, quieter, and far more efficient.
What is an e-power powertrain?
An e-Power powertrain, popularized by Nissan, is a hybrid system where the electric motor always drives the wheels, but a small gasoline engine works only as a generator to recharge the battery. It’s different from traditional hybrids because the engine never powers the wheels directly. The result is an EV-like driving experience—smooth, responsive, and quiet—without requiring external charging.
What is the EV drivetrain system?
The EV drivetrain is a subset of the powertrain that focuses specifically on components that transfer power from the motor to the wheels. This typically includes the motor, reduction gear (transmission), drive shafts, and differentials (if applicable). While the powertrain includes energy generation and control systems, the drivetrain is all about delivering that motion efficiently to the road.
What does powertrain mean in vehicles?
In general automotive terms, the powertrain refers to all systems involved in generating propulsion and transmitting it to the wheels. For combustion vehicles, this includes the engine, transmission, and differential. In electric vehicles, it includes the electric motor, inverter, battery, and all related control systems. The powertrain essentially determines how the vehicle moves and responds to the driver.
What is powertrain vs drivetrain?
The powertrain encompasses both the energy source (engine or electric motor) and the system that delivers power to the wheels. The drivetrain, on the other hand, includes only the components that transfer that power—such as the gearbox, axles, and driveshafts. Think of the powertrain as the whole engine-to-wheel ecosystem, while the drivetrain is the second half of that equation.